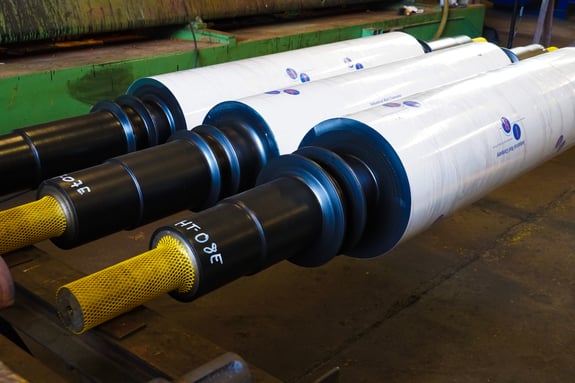
Industrial Roll Formulations
Our innovation originated with the groundbreaking formulation VINACAR released in 1970 as a covering for a coil buggy roll that replaced a competitor’s polyurethane in a stainless steel pickle line. The second generation VINACAR II was developed a few years later and added much improved high-temperature resistance for rolls under greater forced dynamic compression in a continuous annealing line at Bethlehem Steel Sparrows Point – there, VINACAR II lasted 3x as long as the incumbent neoprene rolls and then displaced this competitor. Shortly after, Industrial Roll expanded to the halogen lines at Sparrows Point where it served both the tin and sheet mills as the sole roller supplier. This began a strong expansion into the Ohio/Pittsburgh/West Virginia area that later moved to a national expansion.
Today, each of our core formulations provided are constructed as variations from the original VINACAR formula. We also regularly adjust these formulations to customize our offering for new customers’ specific applications.
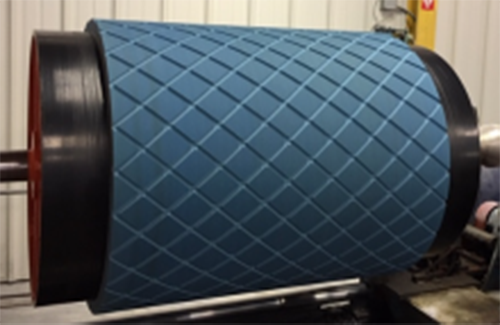
Skytech
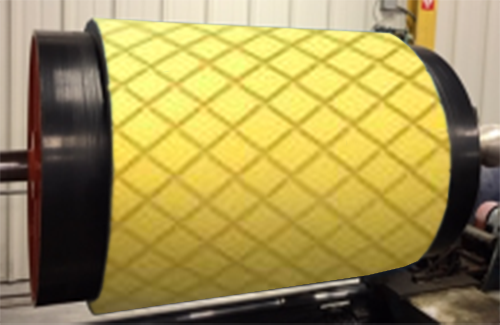
N.Dal (65)
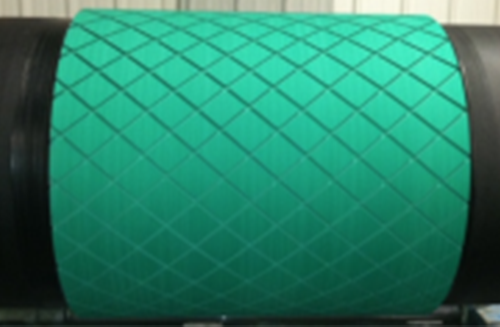
VINACAR III PBU (75)
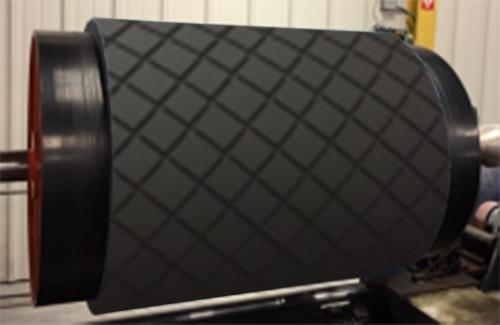
AR-6 (80)
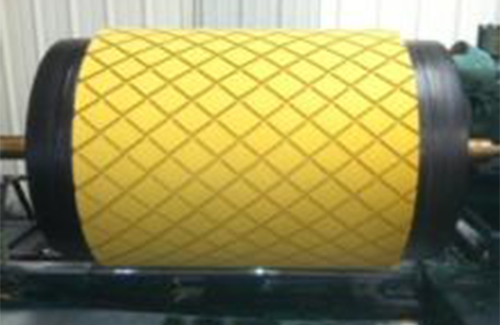
VINACAR II (80)
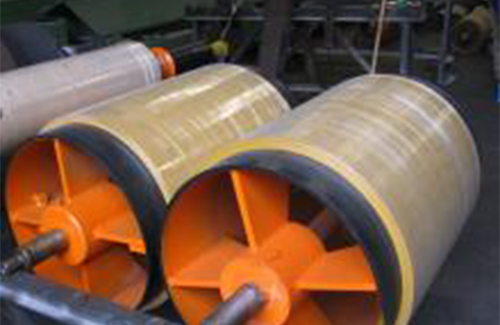
Vinacar HT (80-85)
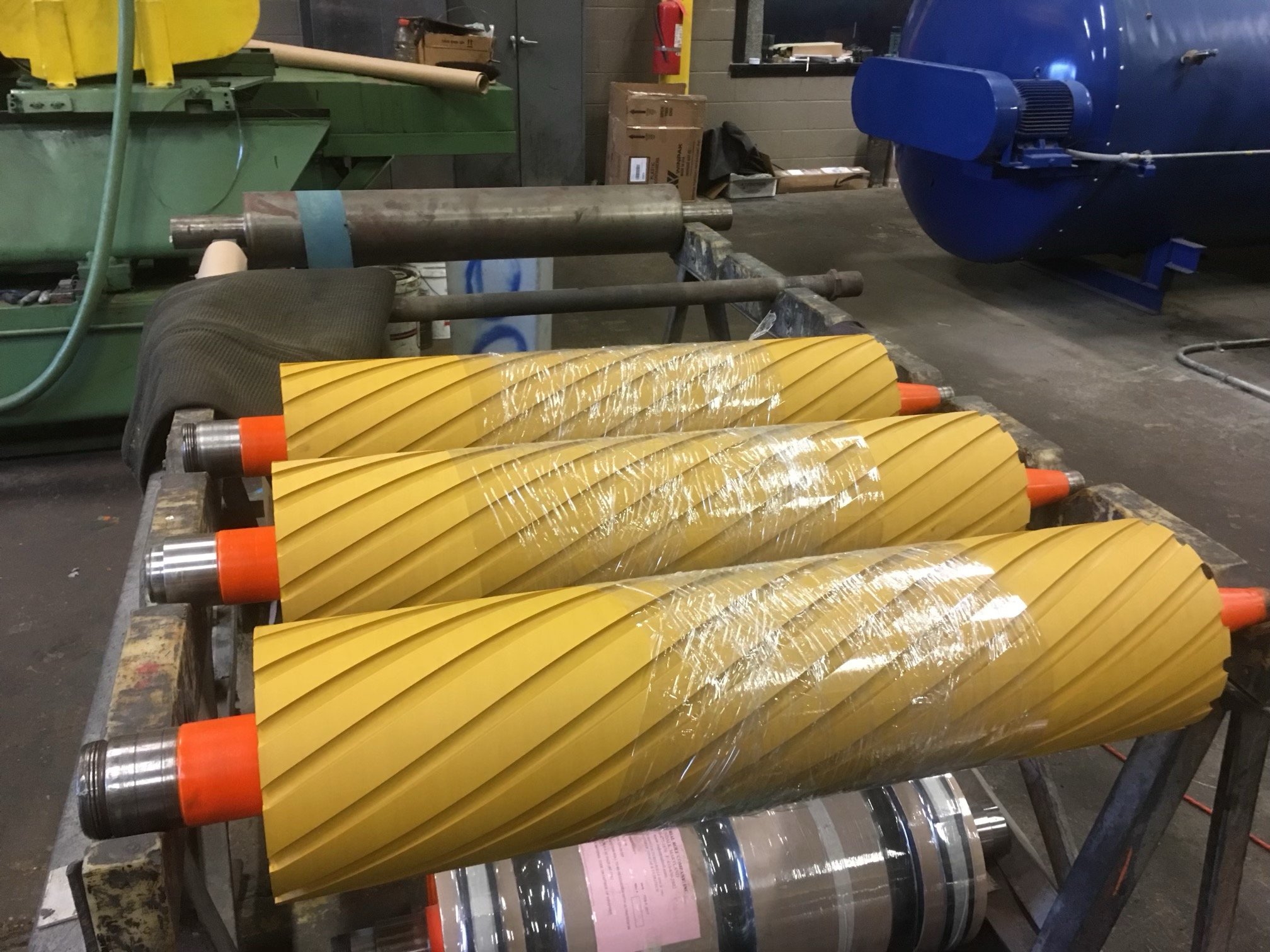
VINACAR Caustic (90)

VINACAR IV ULTRATECH (95)
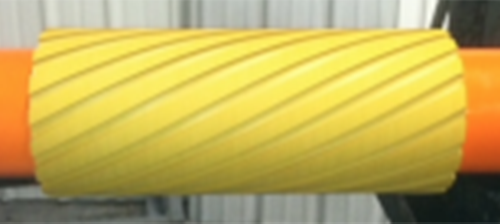